Rapid-Setting Cement: When Speed Matters in Construction
08.07.2025
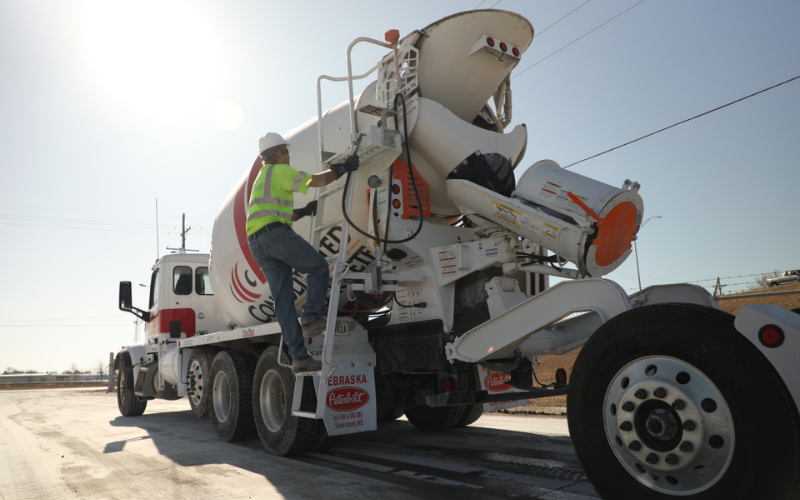
Time is often the most critical factor in construction projects, especially in emergency repairs, infrastructure maintenance, or fast-paced commercial developments. Traditional cement formulations, while reliable, require extended curing periods that can slow down progress and increase labor costs. This is where rapid-setting cement proves invaluable.
Rapid-setting cement, also known as fast-setting or quick-setting cement, is designed to achieve high early strength in a short amount of time. This article explores what rapid-setting cement is, how it works, its advantages, common applications, and important considerations for its use in modern construction.
1. What Is Rapid-Setting Cement?
Rapid-setting cement is a special type of cement that sets and gains strength much faster than ordinary Portland cement (OPC). While typical cement may take 24 to 48 hours to set and several days to cure fully, rapid-setting cement can achieve significant strength within just a few hours—or even minutes in some formulations.
This fast performance is achieved through a modified chemical composition, which may include higher proportions of calcium aluminate, calcium sulfoaluminate, or special additives. These ingredients accelerate hydration and reduce the time required for the material to harden and become load-bearing.
2. How Does Rapid-Setting Cement Work?
The setting and hardening of cement depend on a chemical reaction with water called hydration. In rapid-setting formulations, this process is intensified by adjusting the cement’s mineral content and reducing particle size to increase surface area.
As a result, water rapidly reacts with the cement particles, producing heat and forming strong crystalline structures. Within 15 to 30 minutes, the material begins to stiffen, and in just a few hours, it can support significant loads.
Unlike traditional cement, rapid-setting types do not rely on long-term curing to reach structural strength, making them ideal for fast-track construction schedules.
3. Key Benefits of Rapid-Setting Cement
Using rapid-setting cement offers a wide range of advantages when speed is a top priority:
- Fast strength gain: Allows structures to be used or loaded in hours instead of days.
- Minimized downtime: Ideal for projects requiring quick reopening, such as airport runways or highway repairs.
- Cold-weather performance: The heat generated during hydration helps prevent freezing in low temperatures.
- Reduced labor costs: Faster work means fewer hours spent on-site and shorter project durations.
- Water resistance: Some formulations offer excellent moisture tolerance, beneficial for underwater or damp environments.
These benefits are particularly attractive in industries where time is money and delays are costly or disruptive.
4. Common Applications of Rapid-Setting Cement
Rapid-setting cement is used across various sectors of the construction industry. Some of the most common applications include:
- Road and highway repairs: Enables lane reopening within hours, minimizing traffic disruption.
- Bridge deck overlays: Reduces downtime during maintenance work and ensures quick restoration of service.
- Airport runway and taxiway repairs: Essential for facilities with tight operational schedules.
- Underwater construction: Works well in wet or submerged conditions where traditional cement may not set properly.
- Emergency structural repairs: Allows rapid patching of damaged columns, beams, or slabs.
- Precast applications: Speeds up mold cycles and accelerates production timelines in prefab factories.
In all these scenarios, speed not only increases productivity but also enhances safety and user convenience.
5. Types of Rapid-Setting Cement
Several types of rapid-setting cement are available, each with unique characteristics suited to different tasks:
- Calcium sulfoaluminate (CSA) cement: Known for ultra-fast setting and low shrinkage. Often used in thin overlays and high-performance repairs.
- High-alumina cement: Offers strong resistance to chemicals and thermal shock. Common in refractory applications and chemical plants.
- Modified Portland cement: Traditional cement enhanced with accelerators and fine particles to shorten setting time.
Choosing the right type depends on factors like setting time, temperature conditions, load requirements, and environmental exposure.
6. Considerations and Limitations
While rapid-setting cement offers clear advantages, it also comes with specific challenges that must be managed carefully:
- Short working time: The quick setting nature leaves little room for error. Workers must be prepared to mix and place the material immediately.
- Mixing precision: Incorrect water-to-cement ratios can affect performance and lead to poor bonding or cracking.
- Limited application area per batch: Rapid hardening restricts how much surface can be covered in one mix.
- Cost: Typically more expensive per unit than traditional cement, although the overall cost may be offset by faster completion.
Proper training, planning, and equipment are essential to harness the benefits of rapid-setting cement effectively.
7. Performance in Various Environments
Rapid-setting cement performs well in diverse environmental conditions, including wet, cold, or high-traffic areas. Its heat-generating properties allow it to cure even when external temperatures are low, making it a favorite in winter construction projects.
Additionally, when properly formulated, it exhibits excellent resistance to freeze-thaw cycles, chloride intrusion, and abrasion. These qualities make it reliable in marine construction, urban infrastructure, and remote field repairs.
8. Environmental and Sustainability Factors
Although rapid-setting cements may have a higher embodied carbon footprint than ordinary cement due to specialized manufacturing, they can also offer sustainability advantages. Shorter curing times reduce energy usage on-site, and quicker turnover means less fuel and labor input per project.
In some cases, rapid-setting cements incorporate recycled industrial materials such as fly ash or slag, contributing to circular construction practices. As demand grows for low-carbon solutions, manufacturers continue to innovate greener rapid-setting formulations.
9. Examples of Rapid-Setting Cement in Action
Real-world applications illustrate the value of rapid-setting cement:
- San Francisco International Airport: Used fast-setting concrete for overnight taxiway repairs, enabling runway reopening by morning.
- Interstate Highway Repairs (USA): Departments of transportation regularly use rapid-setting mixes to patch potholes and restore lanes within hours.
- Underground transit tunnels: Rapid-setting mortar and grout ensure stability in wet, unstable environments during rail installation.
These examples highlight how rapid-setting cement minimizes disruption and maintains service continuity in critical infrastructure.
10. Best Practices for Using Rapid-Setting Cement
To achieve the best results when working with rapid-setting cement, consider these best practices:
- Prepare and clean the substrate thoroughly before application.
- Use proper mixing tools to ensure uniform consistency and avoid lumps.
- Only mix what can be placed within the product’s working time.
- Apply in small sections and finish quickly before initial set begins.
- Protect the surface from rapid drying or freezing during the early hours.
Following manufacturer guidelines and training workers in advance will lead to higher success rates and better structural performance.
Conclusion
Rapid-setting cement is a transformative material in the construction industry, offering unparalleled speed, efficiency, and convenience in time-sensitive applications. Whether for emergency infrastructure repairs or high-speed construction schedules, its advantages are clear and impactful.
By understanding how and when to use rapid-setting cement, contractors and engineers can unlock faster project delivery without sacrificing quality or safety. As urban demands grow and timelines tighten, rapid-setting cement proves that speed doesn’t have to come at the expense of performance.